Following the tire manufacturing process exists a convenient piece of equipment, tire uniformity grinding. This underutilized tool allows manufacturers to improve tires on the spot before final tire analysis. Keep reading to explore what tire grinding includes and the various types of grinding available.
What is Tire Uniformity Grinding?
Tire uniformity grinding is a precise final finishing technique for creating high-performance tires. At its core, uniformity grinding abrades the tire tread and sidewall to correct inadequacies and inconsistencies during manufacturing. These inconsistencies may include variations in tread thickness, sidewall stiffness, and other structural irregularities that can compromise tire performance and safety.
Phase 1: Where to Begin?
To fully grasp tire grinding, discussing the tire manufacturing process is essential. Initially, various rubber compounds and additives are blended to each brand’s preference. As the tire takes shape, alternating layers of rubber and a single steel layer are integrated. Subsequently, the tire undergoes heating and pressing within a mold to acquire its definitive form. Following this stage, the tire undergoes quality assessments, during which grinding can be pivotal.
Phase 2: Tire Grinding Takes Place
The grinding process begins with final finishing equipment, including tire uniformity and geometry. Highly accurate assessments of individual tires' characteristics flood in from these machines. Based on measurements including tread depth, sidewall integrity, and tire roundness, the tire uniformity final finish machine identifies areas requiring adjustment and proceeds to the tire uniformity grinding stage.
Phase 3: Down the Line
Uniformity machines equipped with grinders refine the tire surface. These machines meticulously grind away excess rubber material, ensuring uniformity and balance across the entire tire circumference. By targeting specific areas of the tire tread and sidewalls, tire uniformity grinding helps eliminate deviations and irregularities, resulting in smoother rides and enhanced performance on the road.
Understanding Center Grinders
Is there only one category of grinder? Certainly not! Among them, we have center grinders, which, as the name suggests, focus on refining the central portion of the tire. Their primary objective is to minimize radial runout and radial force variation, two critical parameters for tire performance. Improved radial runout is essential for achieving optimal tire roundness. This enhances driving comfort and superior vehicle handling, especially during demanding road conditions.
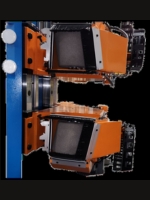
How do Shoulder Grinders Compare?
Is there only one category of grinder? Certainly not! Among them, we have center grinders, which, as the name suggests, focus on refining the central portion of the tire. Their primary objective is to minimize radial runout and radial force variation, two critical parameters for tire performance. Improved radial runout is essential for achieving optimal tire roundness. This enhances driving comfort and superior vehicle handling, especially during demanding road conditions.
Win-Win
The benefit? Not only do the grinding results offer a smoother ride for users, but it also allows manufacturers to decrease costs by reducing scrap tires. Tire uniformity grinding can help fulfill quality measurements prior to tire and wheel assembly machines. By addressing performance issues during quality measurement testing, tire uniformity grinding plays a crucial role in crafting high-quality tires that deliver exceptional driving experiences. As technology advances and manufacturing processes evolve, tire uniformity grinding is expected to increase in importance in years to come.